Business use cases
Empowering Innovation in Aerospace & Defence industries
DECADE-X is dedicated to creating a collaborative ecosystem for data exchange for the aerospace and defence industries, enabling shared insights and driving innovation. Through this ecosystem, critical industry challenges are being addressed by exploring various business use cases across four key business domains.
Supply Chain Resilience
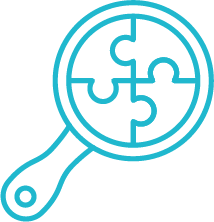
Managing demand and capacity in the aerospace industry poses significant challenges, particularly when dealing with missing parts and supply chain disturbance. The ecosystem must adapt to a multitude of tools and formats of demand data, with existing standards underutilised—especially by Small and Medium-sized Enterprises (SMEs).
This use case aims at harmonising demand and capacity management through a multi-tier approach that integrates and maximises information exchange among all supply chain partners.
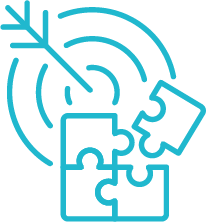
The solution focuses on three core challenges: reducing manufacturing flow disruptions, ensuring consistent and reliable online data exchange, and simplifying data integration through standardised processes. By cascading demand and capacity information across the supply chain, this system provides a consolidated view of multi-customer demand and multi-supplier capacity, ensuring greater inventory visibility and reducing inefficiencies (missing parts, flow disruptions…). Key benefits include streamlined workflows, reduced data consolidation efforts, enhanced collaboration, and improved alert mechanisms to address missing parts and anticipate forecasts.
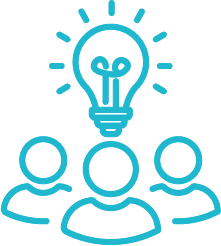
This approach guarantees data security and sovereignty while enabling seamless communication across the aerospace and defence value chain, able to cover commercial and military businesses, cross functions, and flying goods. It applies to Original Equipment Manufacturers, Tier 1-n suppliers, and SMEs. Key users such as supply officers, planners, risk managers, and sales managers benefit from better decision-making tools, reduced non-conformities, and an optimised production flow.
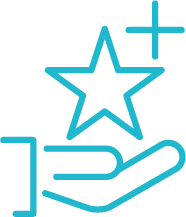
By fostering standardisation and collaboration, this use case transforms the aerospace and defence ecosystem into a more efficient, reliable, and resilient network so as to manage demand and capacity.
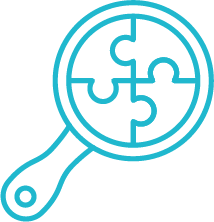
The Quality Management business use case addresses the critical challenge of navigating an ecosystem with non-conformity across data sharing. Aerospace and Defence companies have to manage diverse tool and data formats across multiple clients, which can lead to inconsistencies and inefficiencies (such as non conformity).
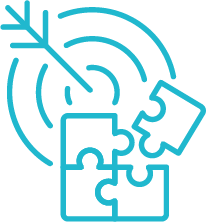
This solution establishes an harmonized, multi-tier quality management system designed to ensure consistent and accurate data management while enabling better analysis, containment, resolution, and prevention actions. By adopting standardized processes and tools, the system reduces the operational complexity, particularly for small and medium enterprises, while fostering a collaborative environment across the supply chain. It accelerates the resolution of non-conformities, provides a consolidated view of quality metrics across clients and suppliers, and improves reporting and analytics for proactive decision-making.
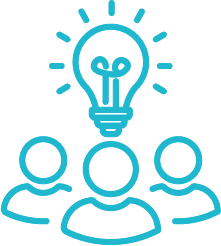
With a strong emphasis on data security and sovereignty, this solution ensures trust and confidentiality at every stage of the quality management process, from containment to corrective and preventive actions. Applicable to the entire value chain—including commercial and military businesses, flying goods, Original Equipment Manufacturers, and Tier 1-n suppliers—the use case supports key roles such as non-conformity managers, risk managers, compliance managers and manufacturing managers.
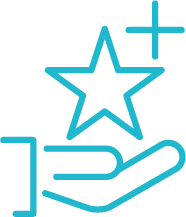
By reducing non-conformities, streamlining workflows, and enhancing transparency, this quality management approach transforms the aerospace industry into a more efficient, reliable, and collaborative ecosystem. It empowers stakeholders to meet demanding quality standards while reducing efforts and fostering trust throughout the value chain.
Traceability
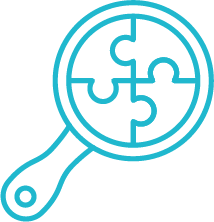
Product conformity and Authorized Release Certificates (ARC) are critical for ensuring traceability throughout the product lifecycle. However, businesses face significant challenges due to scattered compliance data and documents across various systems, including Certificate of Conformities, EASA Form 1 and paper records. Ensuring traceability and securing data exchanges, especially for military products, adds to the complexity.
Two primary challenges have been identified: enabling consistent and accurate data management and providing and collecting data through a tool based on standard processes.
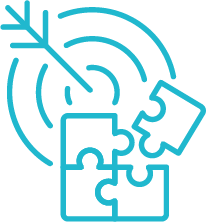
This use case aims at ensuring the traceability of logistics and compliance documents all along the product lifecycle. This ensures full transparency, efficient management, and secure sharing of information across the whole supply chain. The business value includes reducing the risk of counterfailed documentation or materials, maintaining version histories, and creating clear links between parent and child components. Real-time sharing of data in a standard format reduces the effort of data collection and accelerates the identification of parts affected by quality issues.
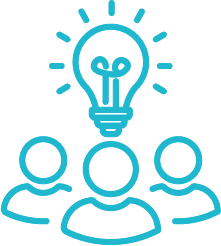
The scope of the use case spans the entire value chain, including commercial and military businesses, cross functions as well as flying goods and Original Equipment Manufacturers at all supply chain levels. Key users include non-conformity managers, logistics teams, certifying staff, and quality managers.
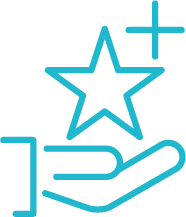
Potential features include the traceability of compliance documents with version control and the ability to search for original documents using metadata. These capabilities enhance transparency, reduce risk, and ensure secure and efficient management of product conformity documentation.
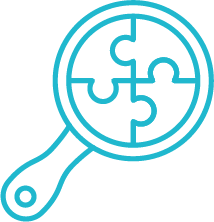
Export control compliance is a complex challenge that requires organisations to comply with a multitude of national and international regulations. Managing export licenses, classifying products and technologies, and verifying destinations and customers are complex processes that require specialized resources.
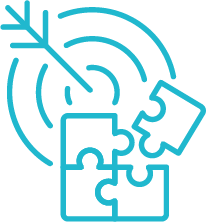
Through this business use case, we are addressing three key challenges: ensuring consistent and accurate classification management, streamlining documentation and licensing management, and simplifying regulatory compliance updates. The objective is to establish a single source of truth for export control data, enabling seamless information sharing and preventing duplicate requests.
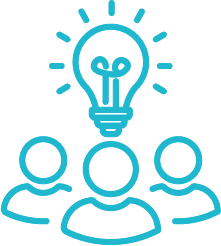
The proposed export Control platform will enhance transparency and operational exchange among Aerospace & Defence stakeholders through workflow automation, real-time screening, and an intuitive User Interface, ensuring regulatory adherence in a simplified and standardized manner. The platform delivers measurable business value by meeting legal compliance requirements, reducing lead times, ensuring data confidentiality and trust, embedding compliance by design, and standardizing data models.
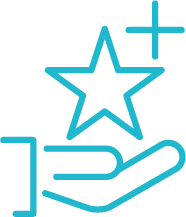
Its scope spans the entire value chain—commercial and military businesses, cross-functional teams, flying and non-flying goods, Original Equipment Manufacturers, and Tier 1-n suppliers.
Key users, including supply chain officers/buyers, legal representatives, business representatives and engineering teams, can benefit from specific features such as the Export Control Classification Workflow Manager. This feature enables export control classification data collections for parts/products and classification workflow management that provides real time status. Additionally, the Export Control Documentation Management secure storage and management of all export control-related documents, manages version control and audit trails for all documents changes and approvals.
Sustainability
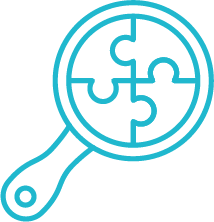
The lack of dedicated sustainability management processes presents a significant obstacle to address carbon footprint challenges across industries. Many small and mid-sized enterprises (SMEs), do not have the capacity to conduct Product Carbon Footprint (PCF) or Life Cycle Assessment (LCA). In the aerospace and defence industry the problem is magnified by the absence of standardized methodologies to measure with accuracy Scope 3 emissions of bought products. This gap is exacerbated by the lack of secure and standardized mechanisms to share PCF and LCA data along supply chain partners.
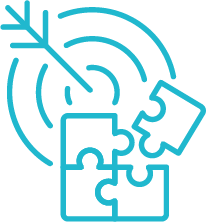
This business use case aims at providing digital means for Small and Medium-size Enterprises to calculate the carbon footprint/LCA of their manufactured products (scope 1 & 2) in a consistent and standardized approach. Also, it aims at obtaining the carbon footprint/LCA of the products purchased by a company in order to be able to easily decline its scope 3 (mandatory). Increasing the transparency and quality of data through a standardized procedure will allow us to manage the carbon footprint/LCA of our aeronautics industry and our processes to minimize global warming of our planet.
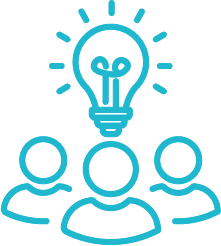
Applicable to the entire value chain—including commercial and military product and services, cross business functions, Original Equipment Manufacturers, and Tier 1-n suppliers—the use case supports key roles such as suppliers, LCA practitioners, Designers, procurement sustainability officers, supply chain officers/buyers and corporate sustainability teams.
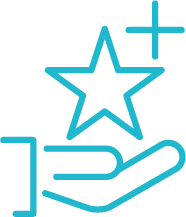
Potential capabilities of the solution include end-to-end integration and exchange of PCFs and LCAs, implementation of calculation processes and integration into digital manufacturing platforms (DMPs), digital product passports (DPPs) and digital twin.
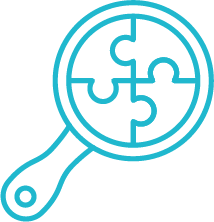
The Circular Economy is becoming a cornerstone of sustainability strategies, yet the aerospace and defence industry face numerous challenges in its implementation.
Today’s regulations emphasize on designing more sustainable products while resources are limited. However, there is no standardized information on product materials, composition, or location, creating significant inefficiencies across the supply chain. The low level of digitalization compounds the problem, leading to time-consuming manual data searches during the middle and end of a product’s lifecycle.
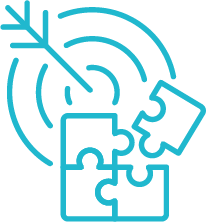
To address these challenges, this business use case aims to set a digital ecosystem that creates efficient feedback loops between all the players. In this way, we will increase the value of unused components and products through improved data availability and logical decision making processes. End to end traceability of components will be integrated while respecting the existing roles and responsibilities within the industry.
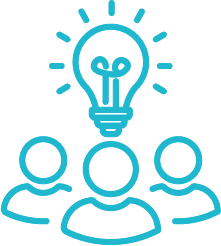
The scope of this initiative spans all aerospace products and services and includes the entire supply chain—Original Equipment Manufacturers, Tier 1, and Tier N suppliers—as well as airlines, MROs, brokers, dismantlers, and recyclers. Key users of this ecosystem include engineering, suppliers, manufacturing, OEM aftermarket, brokers, and dismantlers.
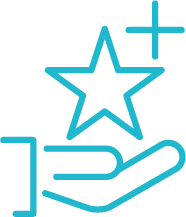
The solution includes implementing decision-making logics for reuse, repair, refurbish, remanufacture, or recycle components, as well as integrating Digital Manufacturing Platforms (DMP) and Digital Product Passports (DPP). Together, these functionalities will enable seamless data sharing, improve component lifecycle management, and ensure that the industry makes significant progress toward a fully circular economy.
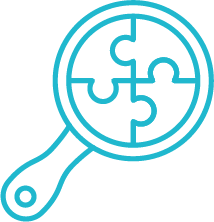
The growing demand for Environmental, Social, and Governance (ESG) reporting presents significant challenges for businesses in the aerospace and Defence sectors. This demand requires considerable efforts to identify, collect, and provide data. The diversity of reporting formats and methodologies across various regulatory bodies further complicates compliance. Additionally, accessing reliable sustainability data from suppliers remains a complex task.
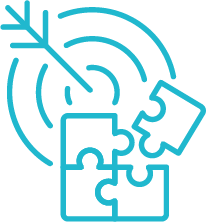
ESG Reporting business use case aims at enabling aerospace and Defence companies to collect, standardize, and share ESG data in a transparent and reliable manner. By facilitating the creation of reports that comply with international regulatory frameworks such as the Corporate Sustainability Reporting Directive (CSRD) and the U.S. Securities and Exchange Commission (SEC) requirements, this solution addresses the critical need for efficient and accurate ESG reporting. The proposed approach reduces the costs and time associated with data collection while ensuring comprehensive compliance with evolving global regulations.
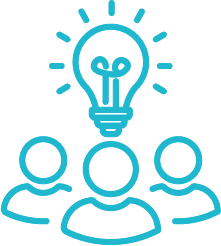
The scope of this use case encompasses the entire global value chain, including all products and services, as well as original equipment manufacturers (Original Equipment Manufacturers) and Tier 1 to Tier N suppliers and extends to manufacturers that use chemicals in their production processes. It is designed to support companies across the aerospace and Defence industry, with particular relevance for organisations in highly regulated regions. Key users include environment managers, compliance managers, risk managers, and sales managers, all of whom play critical roles in ensuring the success of ESG initiatives.
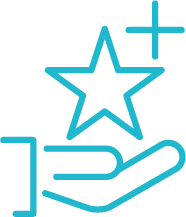
The solution’s primary features include the collection and aggregation of ESG data, as well as capabilities for reporting and performance monitoring aligned with the CSRD and other global standards. This approach not only facilitates regulatory compliance but also strengthens companies’ contributions to sustainable development and responsible business practices.
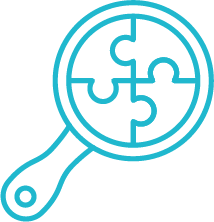
Substance tracking is a critical component of sustainability, yet it presents several challenges for businesses. Data is often scattered across various sources, including vendor documentation, internal databases, and external regulatory websites. This fragmentation complicates data management and creates inconsistencies in data formats and quality, hampering accurate analysis and reporting. Additionally, the manual collection and processing of substance data are time-consuming, error-prone, and resource-intensive. To address these issues, we need to ensure consistent and accurate data management and establish a standardized, tool-based process.
Substance tracking use case aims at automating the collection and processing of substance data in the supply chain to reduce manual efforts and ensure traceability.
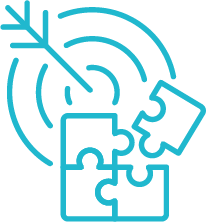
This approach reduces costs and delays associated with achieving transparency in compliance. It improves responsiveness to regulatory updates, minimizes the risk of non-compliance, and increases overall transparency across the supply chain.
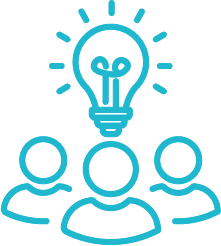
The scope is broad, encompassing the entire global value chain, including all products and services, as well as original equipment manufacturers (Original Equipment Manufacturers) and Tier 1 to Tier N suppliers and extends to manufacturers that use chemicals in their production processes. It is designed to support companies across the aerospace and Defence industry, with particular relevance for organisations in highly regulated regions such as Europe and the United States. Key users include environment managers, compliance managers, sustainability procurement managers, and substance managers.
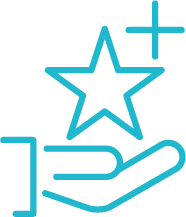
The solution’s two main features focus on collecting and providing substance data through standardized reports and leveraging data analysis and processing through Data Quality checks. By implementing a tool-based approach to substance tracking, organisations can create a more resilient and sustainable supply chain.
Design & tech data
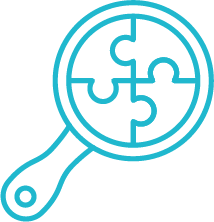
Efficient design and technical data exchange is critical for staying competitive in the fast-paced aerospace and Defence sector. However, businesses face several challenges that hinder seamless collaboration. Lengthy and sequential contractual, Intellectual Property (IP) and IT integration steps hinder rapid collaboration. Responding quickly to fast-evolving market needs becomes challenging.
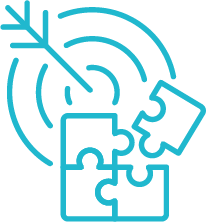
This use case aims at establishing a seamless, secure, and efficient collaborative ecosystem. This system will enable rapid onboarding of partners, real-time co-design capabilities, and streamlined data exchange processes. By implementing these measures, we will reduce time-to-market for aerospace products while ensuring competitiveness.
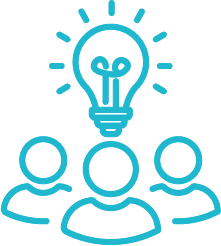
The business value of this initiative lies in its ability to reduce the time required to set up the IT environments needed for partner collaboration. Effective data sharing will decrease product development time and costs, enabling faster delivery. Joint optimization capabilities will improve product architecture and performance. Enhanced relationships between industrial partners at the working level will foster greater collaboration and trust.
Applicable to the entire value chain—including commercial and military businesses, flying goods, Original Equipment Manufacturers, and Tier 1-n suppliers—the use case supports key roles such as customer and supplier engineering teams, research partners, and regulation authorities.
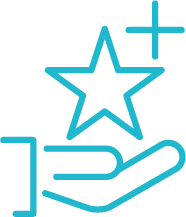
The proposed solution will provide a collaborative workspace that supports real-time co-editing of designs and specifications. It will also enable data exchange and integration, ensuring secure file sharing with granular access controls. Together, these capabilities will create a foundation for faster product development and competitive advantages in the aerospace market.
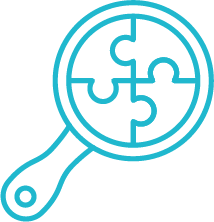
The requirement cascading process is a cornerstone of product development in complex industries like aerospace and defence, yet it faces numerous challenges. Significant delays occur during the alignment of specifications between suppliers and customers in co-development phases. Defining clear responsibilities of customers versus suppliers is difficult. In addition, the lack of standardized tools covering the entire process complicates effective requirements management.
Requirement cascade use case aims at facilitating the collaborative management of complex engineering (or others) requirements. By enabling full traceability and reducing time to market, this approach seeks to optimize product architecture while improving overall efficiency.
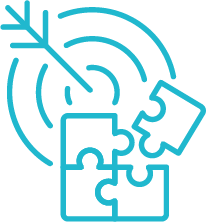
This approach delivers significant business value such as reducing the development time of new products. The standardization of reference elements (e.g subsystem specification standards), improves consistency and simplifies the collaboration process. Increased transparency and traceability throughout the product lifecycle minimize the risk of errors in the interpretation of requirements, enhancing overall reliability.
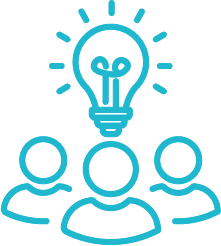
The scope is broad, spanning the entire value chain. It applies to both commercial and military businesses, covering all business functions and encompassing both hardware and software products. It is relevant for Original Equipment Manufacturers, Tier 1 to Tier N suppliers, and companies actively contributing to product design. Key users of this solution include sales managers, multifunctional teams, buyers, and regulatory authorities.
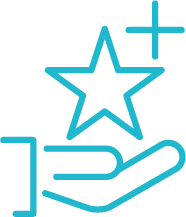
The solution offers two critical features. The first is a collaborative space for the management and cascading of requirements, which allows stakeholders to collaborate and break down into specific requirements. The second feature focuses on traceability and version control of requirements by guaranteeing access to the latest version of the requirements. Together, these capabilities address the challenges of requirement cascade, enabling faster, more efficient, and more reliable product development in complex industries.